transfluid® t cut TYPE RTO
Created for precision.
There are many good reasons to separate tubes chiplessly. And first of all, of course, the cleanliness. Precision and output, too, are not insignificant. Our chipless orbital cutting machines make precise cutting results possible. Your tubes can be formed immediately afterwards. That saves time and money.
Technical specifications:
- Separation efficiency: max. Ø 30 x 3 for stainless steel tubes
- Shortest separation length:
- 25 mm (without pull apart)
- 55 mm (with pull apart) - Remaining length: 110 mm
- Separation efficiency: up to 2,000 pcs per hour
PERFECT CUTS WITH THE GREATEST PRECISION
All transfluid machines deliver the highest cut quality and the workpieces can be processed without any further steps.
The right machine for your task
RTO CUTTING MACHINES
Max. capacity | 1/4" - 1 1/8" in |
Wall thickness | .072" in |
Shortest cutting lenght (pull apart) | 2.1" in |
Shortest cutting lenght (through cut) | 1" in |
Cycle time adjustable | 2.2 - 8.0 sec. |
Power | 7 kW |
Weight | 3740 lb |
L x W x H | 110 x 41 x 63 in |
Max. capacity | 1/4" - 2" |
Wall thickness | .095" |
Shortest cutting lenght (pull apart) | 2.1" |
Shortest cutting lenght (through cut) | 1" |
Cycle time adjustable | 2.2 - 8.0 sec. |
Power | 7 kW |
Weight | 3740 lb |
L x W x H | 110 x 41 x 63 in |
Max. capacity | 3/4" - 3" |
Wall thickness | .120" |
Shortest cutting lenght (pull apart) | 3.9" |
Shortest cutting lenght (through cut) | 2.7" |
Cycle time adjustable | 5 - 10 sec. |
Power | 10 kW |
Weight | 6600 lb |
L x W x H | 150 x 55 x 63 in |
Max. capacity | 3/4" - 4" |
Wall thickness | .120" |
Shortest cutting lenght (pull apart) | 6.7" |
Shortest cutting lenght (through cut) | 3.9" |
Cycle time adjustable | 5 - 10 sec. |
Power | 15 kW |
Weight | 9020 lb |
L x W x H | 122 x 51 x 65 in |
PREPARED FOR INTEGRATION INTO PRODUCTION CELLS
Whether as a stand-alone machine or as production cell, the t cut machines are above the rest thanks to the easy operation and accurate results!
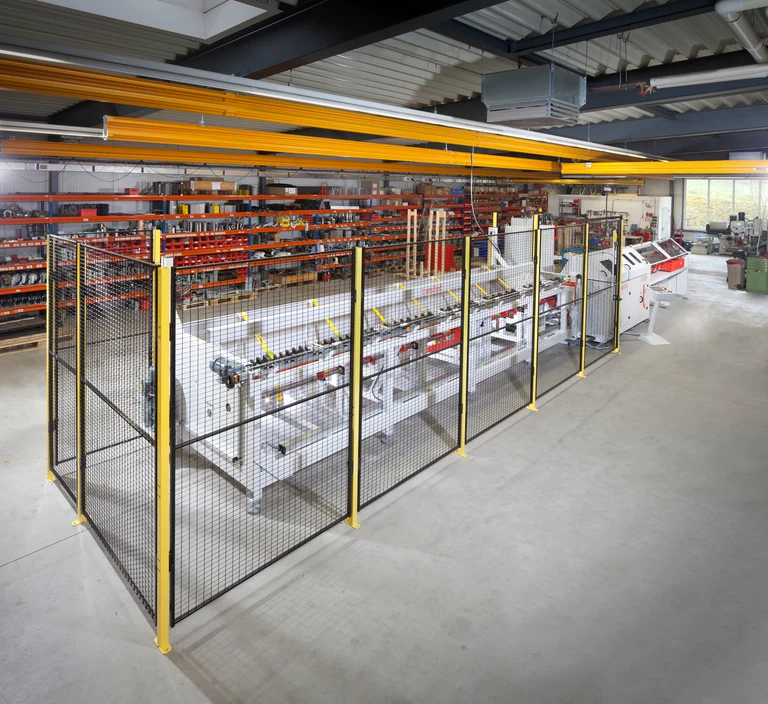
A COMPELLING OPTION FOR CLEAN CUTTING RESULTS
All transfluid machines deliver the highest cut quality and the workpieces can be processed without any further steps.
Catalog Download
transfluid® offers the complete package for the production of tubing.
Download our new catalogue.
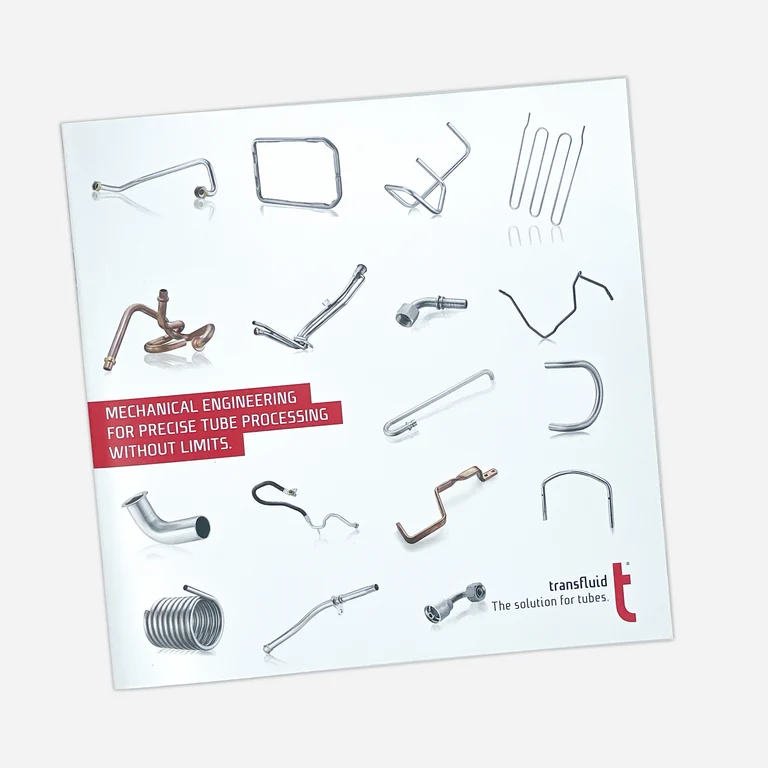